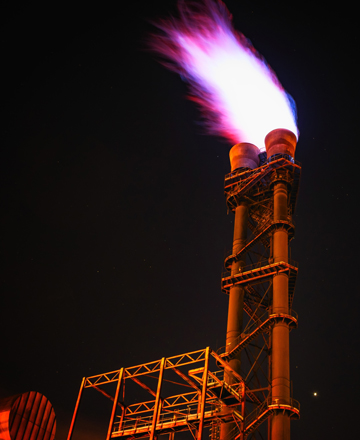
- فروردین 22, 1399
- adminiMahi
- دستهبندی نشده
- ۰ Comments
چکيده
با عنايت به تحولات چشمگير در صنعت خودروسازي در بخش خودروهاي کار و موفقيت شرکت هاي خودروساز کشور در تبديل سوخت انواع اتوبوس ، ميني بوس، کاميون و کاميونت از گازوئيل به عنوان يکي از سوختهاي آلاينده ودر عين حال با ارزش به گاز طبيعي، کاربرد وسيع مخازن CNG و مسائل مربوط به آن از جمله خوردگي مخازن نامبرده به عنوان يکي از دغدغه هاي اساسي صنعتگران و کاربران مطرح مي باشد. استفاده از گاز طبيعي به صورت سوختي با آلودگي كم ، نسبت به بنزين ، گازوئيل و پروپان بصورت روزافزون در سطح دنيا در حال افزايش است . دلايل اصلي استفاده از اين سوخت در بعضي از كشورها كاهش هزينه ، كاهش آلودگي و افزايش ايمني به همراه اطمينان از طولاني بودن مدت مصرف و تامين آن مي باشد.
پژوهش حاضر سعي بر تحليل خوردگي هاي متداول در مخازن گاز CNG دارد. در اين مقاله خوردگي
يکنواخت ، خوردگي حفره اي ، خوردگي توام با تنش (SCC ) در مواردي که مخزن در معرض تعداد زيادي سيکلهاي فشار و نيز سيال خورنده قرار مي گيرد ، اثر خوردگي گالوانيکي هنگامي که در مخازن تيپI ، II و III فلز تشکيل دهنده مخزن در تماس با محافظ فلزي خود مي باشند ، خوردگي سايشي مربوط به لايه کامپوزيتي مخزن در اثر شرايط محيطي و کاري ، و اثر ترکيبات گاز مانند ترکيبهاي گوگرد ، هيدروژن ، دي اکسيد کربن و آب بر روي تسريع در عمل خوردگي مورد تحليل قرار مي گيرد و در آخر نيز به ارائه راهکارهايي براي جلوگيري و کنترل اين عوامل خواهيم پرداخت.
کليد واژه : خوردگي مخازن CNG – خوردگي گالوانيک – خوردگي توام با تنش – مخازن CNG
- کارشناس ارشد شيمي
- کارشناس مهندسي متالورژي
مقدمه
تغيير نوع سوخت خودروهاي کار از گازوئيل به گاز طبيعي به عنوان بخشي از برنامه های استراتژيک شرکت ايران خودرو ديزل زمينه ساز آغاز تحقيقات و مطالعات تخصصی در شرکت توسعه خودروکار بوده است. مخازن ذخيره سازي CNG يکي از مهمترين بخش هاي سيستم گاز در خودروهاي گازسوز مي باشد که بدليل شرايط کاري مخازن ، بايستي ضريب ايمني آنها در طراحي و ساخت بسيار بالا باشد . اينگونه مخازن که در چهار
نوع I , II ,III وIV دسته بندي مي شوند از مواد فلزي و يا غير فلزي (کامپوزيتها) و يا ترکيب آنها ساخته
مي شوند که طراحي و ساخت آنها داراي مراحل پيچيده اي ميباشد . مخازن CNG بايستي حتي الامکان سبک بوده وتوانايي بارهاي خستگي در شرايط محيطي مختلف ودر مواقعي که داراي آسيب نيز هستند را داشته باشند.
خوردگي در مواد مهندسي يکي از مهمترين مسائلي مي باشد که علاوه بر پديدآوردن مشکلات اقتصادي ، زيست محيطي ، فني ، ايمني و … بخش قابل ملاحظه اي از تحقيقات و پژوهش هاي صنعتي را به خود اختصاص داده است. افزايش قيمت انرژي ، نيروي انساني ، فشارها و دماهاي بالا و محيط هاي خورنده تر و پيچيده تر در فرآيندهاي صنعتي باعث مي شوند که زيان هاي اقتصادي ناشي از خوردگي در سالهاي آتي بطور تصاعدي افزايش يابند. اهميت خوردگي در صنايع هنگامي فزوني پيدا مي کند که اثرات سوء آن بطور مستقيم امنيت کاربران را تهديد کند . از جمله مواردي که تهديد خوردگي را متوجه خود داشته و اين تحقيق سعي بر بررسي آن دارد مخازن CNG ( Compressed Natural Gas ) ويژه ذخيره سازي گاز طبيعي خودروهاي گاز سوز است.
بررسي ترکيبات موجود در گاز طبيعي
گاز طبيعي مخلوطي از متان (حداقل 82%حجم ) ، اتان (حداكثر 12% ) پروپان (حداكثر 4% ) ، بوتان و هيدروكربن هاي سنگين تر (حداكثر 4/1% ) وبقيه شامل گازهاي غير سوختي ازت و دي اكسيد كربن ميباشد . البته مطابق اطلاعات واصله از شركت ملي گاز ايران ، ميزان سولفيد هيدروژن ( H2S ) بين صفر و 5 ميلي گرم بر متر مكعب در شرايط استاندارد گزارش شده است . تركيبات تشكيل دهنده گاز طبيعي مي تواند از يك منبع به منبع ديگر و از يك محل به محل ديگر در زمان هاي مختلف تغييركند . بدليل بي رنگ و بي بو بودن گاز طبيعي ، به منظور تشخيص نشت وجلوگيري از هر گونه خطر احتمالي ، به آن 2% پنتان ( C5H12) ويا مقداري اتيل مركاپتان كه بوئي شبيه سير دارد مي افزايند . به خاطر سبك بودن گاز طبيعي نسبت به هوا در صورت نشت ، در قسمتهاي پايين جمع نشده وخطر آفرين نيست . دماي تبخير متان واتان به ترتيب 162- و 102- درجه سانتيگراد ميباشد . درجدول ( 1 )و (2 )آناليز گاز طبيعي و مشخصات فيزيکي آورده شده است.
جدول1- آناليز گاز طبيعی
مقدار مجاز |
Mole% |
Formula |
Component |
MIN. 82.0 |
87.77 |
CH4 |
Methane |
MAX. 12.0 |
4.36 |
C2H6 |
Ethane |
MAX. 4.0 |
1.38 |
C3H8 |
Propane |
MAX. 1.0 |
0.29 |
i-C4H10 |
i-Butane |
MAX. 1.0 |
0.42 |
n- C4H10 |
n- Butane |
MAX. 0.4 |
0.17 |
i-C5H12 |
i-pentane |
MAX. 0.4 |
0.11 |
n- C5H12 |
n-pentane |
MAX. 0.4 |
0.26 |
C6H14 |
n-Hexane & Heavier |
MAX. 2.0 |
0.03 |
CO2 |
Carbon Dioxide |
MAX. 5.5 |
5.21 |
N2 |
Nitrogen |
100 |
Total |
مقدار مجاز |
mg / SM3 |
Component |
MAX. 5.0 |
1.36 |
H2S |
MAX. 15.0 |
14.86 |
Mercaptane |
جدول2- مشخصات فيزيکي گاز طبيعی
وزن ملکولی |
33/18 |
چگالی نسبی |
6385/0 |
ارزش حرارتی ناخالص( KCal / SM3) |
2/9323 |
مقدار مجاز حرارتی ناخالص( KCal / SM3) |
9400-8700 |
نقطه شبنم هيدروکربنی در فشار7/66 بار نسبی |
15- درجه سانتی گراد |
مقدار مجاز در فشار 55 بار مطلق |
10- درجه سانتی گراد |
مقدار آب همراه مقدار مجاز آب همراه ماکزيمم |
Kg/MMSCM 77 Kg/MMSCM 45 |
مشخصات گاز طبيعي فشرده (CNG )
- وزن مخصوص آن نسبت به هوا در فشار يك اتمسفر و دماي 15 درجه سانتيگراد در حدود 65/0 است.
- درجه حرارت اشتعال گاز طبيعي 630 درجه سانتيگراد (درجه حرارت اشتعال بنزين 450 درجه سانتيگراد ) مي باشد.
- حد پايين و حد بالاي اشتعال گاز طبيعي در فشار يك اتمسفر ، به صورت درصد حجمي گاز طبيعي در مخلوط هوا به گاز ، به ترتيب برابر 5 و 15 درصد مي باشد.
- ارزش حرارتي يك متر مكعب گاز طبيعي در فشار يك اتمسفر و درجه حرارت 15 درجه سانتيگراد تقريبا برابر 000/10 كيلو كالري بر متر مكعب (ارزش حرارتي بنزين 9000 كيلو كالري بر ليتر
مي باشد . ) - براي سوختن يك حجم گاز طبيعي به 10 تا 11 حجم هوا نياز است .
- عدد اكتان گاز طبيعي 130 ( عدد اكتان بنزين حدود 90 ) است .
تجهيزات گازسوز به دليل کار در شرايط فشار بالا از حساسيت ايمني بيشتري برخوردار هستند. مخازن تحت فشار گاز طبيعي CNG که در وسايل نقليه سبک و سنگين مورد استفاده قرار مي گيرند بايستي از قابليت اطمينان کافي براي مصرف کننده برخوردار باشند . چهار نوع مخازن CNG وجود دارند که بطور خلاصه در ذيل به آن اشاره مي گردد.
- مخازن CNG نوع اول – فلزي : CNG-1(All metal )
گرچه نوع آلياژ مورد استفاده و همچنين تنش هاي طراحي اين گونه مخازن در استاندارد مشخص نشده است وليكن اين گونه مخازن فولادي يا آلومينيومي بايد تست هاي كارايي را بگذرانند . اين تست ها براي اطمينان از مقاومت كافي اين مخازن در مقابل خستگي وخوردگي لازم است . ايمني اين مخازن با انواع آزمايشهاي غيرمخرب از قبيل سختي ، تست فشار هيدرواستاتيك و … تعيين مي گردد.
جنس لوله هاي فولادي معمولا ازجنس آلياژ نوع 34 Cr Mo 4 مي باشد.
- مخازن CNG نوع دوم . CNG-2(Hoop Wrapped )
اين مخازن از فولاد يا آلومينيوم ساخته شده اند كه با الياف كامپوزيت در جهت شعاعي تقويت شده اند( به جز دو قسمت ابتدائي و انتهايي مخزن ).درشكل ( 1 ) اين نوع مخزن نشان داده شده است.
کامپوزيت های مورد استفاده در مخازن CNG عموماً از الياف شيشه ، کربن يا آرميد با رزين اپوکسي و يا رزين ايزو فتاليک پلي استر مي باشند.
شکل 1- مخازن CNG نوع دوم
- مخازن CNG نوع سوم . CNG-3(Fully Wrapped )
اين مخازن از فولاد يا آلومينيوم ساخته شده اند كه با الياف كامپوزيت در جهت شعاعي و محوري تقويت شده اند شکل ( 2 ) . تقويت اين مخازن با الياف كامپوزيت در دو جهت ، قابليت تحمل فشار بيشتري را نسبت به مخازن نوع دوم ميدهد و همچنين اين مخازن سبكتر از مخازن نوع دوم مي باشند .
شکل 2 – مخازن CNG نوع سوم . CNG-3(Fully Wrapped)
- مخازن CNG نوع چهارم . CNG-4(All composite )
اين مخازن مشابه مخازن نوع سوم با الياف كامپوزيت در جهت شعاعي و محوري تقويت شده اند ، با اين تفاوت كه ديواره ( لاينر ) مورد استفاده در اين مخازن از موادپليمري (مانند پلي اتيلن ) ميباشد .
شکل ( 3 ) مقطع طولي مخزن تيپ IV رانشان ميدهد.
شکل 3- مقطع طولي مخازن CNG نوع چهارم . CNG-4(All composite )
شرايط بهره برداري مخازن
فشار كاري اين مخازن bar200 در دماي 15 درجه سانتيگراد مي باشد . حداكثر فشار پركردن اين مخازن bar260 است كه اين ميزان بيشتر از فشار قابل قبول در حين پركردن سريع مي باشد . حداقل تعداد دفعات پركردن اين مخازن 15000 بار براي حداكثر فشار پركردن مي باشد .
مشكلات انتخاب گاز
لازمه انتقال و ذخيره سازي آن به صورت گاز طبيعي فشرده ( CNG) كنترل تركيب گاز مي باشد . در حالت كلي اگر تركيب گاز طبق ضوابط خاصي در خطوط لوله جريان يابد ذخيره سازي آن مشكلي نخواهد داشت .
استاندارد ISO مربوط به مخازن هاي فشار بالاي ذخيره گاز طبيعي (1996) در مورد مقدار سولفيد هيدروژن
( H2S ) ، سولفور ، دي اكسيد كربن ( CO2) و اكسيژن محدوده اي را مشخص كرده است كه در جدول(3) آورده شده است .
جدول-3 مقدار سولفيد هيدروژن ( H2S ) ، سولفور ، دي اكسيد كربن ( CO2) و اكسيژن
مطابق استاندارد ISO (1996)
23 mg/m3 |
H2S (شامل مر كاپتان نيز مي شود) |
460 mg/m3 |
سولفور |
3% حجمي |
CO2 |
1% حجمي |
O2 |
تاثير گازهاي فوق وديگر گازها در انتقال و ذخيره سازي به طور جداگانه بررسي مي گردد.
- آب
هنگامي كه گاز طبيعي فشرده شود ، بجز مواردي كه گاز بسيار خشك است نقطه شبنم گاز افزايش مي يابد . بدين ترتيب آب در خط لوله و مخازنهاي CNG بوجود مي آيد . در فصل زمستان احتمال وقوع اين مشكل افزايش مي يابد . وجود آب مي تواند باعث خوردگي و بوجود آمدن تركيبات بازي شود .
- دي اكسيد كربن
وجود CO2 در گاز داخل مخازن فولادي كه در معرض آب نيز باشند باعث تشكيل FeCO3( كربنات آهن (II) ) مي شود . سرعت خوردگي بسته به فشار ، دما ، غلظت و مقاومت لايه ها دارد. خوردگي مي تواند صرفا محدود به نقاطي شودكه آب جمع شده است .
- تركيبات هيدراته
با افزايش فشار درون مخازن هيدراتها ميتوانند در دماهاي بالاتر از صفر درجه تشكيل شوند . اين امر ميتواند باعث مسدود شدن لوله ها ، شيرها ، رگولاتورهاي فشار وشيرهاي ايمني شود . به همين دليل عموما يك محدوده مجاز براي مقدار آب موجود در مخازن تعريف مي كنند . غلظت آب بايد به قدري كم باشد كه نقطه انجماد در فشار bar200( bar1= atm986/0 ) ، 5 درجه سانتيگراد كمتر ازحداقل دماي محلي باشد . در عمل اين به معني مجاز بودن مقدار آب تا 50-10 ميليگرم بر متر مكعب مي باشد .
- سولفيد هيدروژن ( H2S )
در صورت وجود آب ، سولفيد هيدروژن ( H2S ) مي تواند بصورت تركيبات اسيدي ظاهر شده و
باعث افزايش خوردگي و تردي فلز شود . مقدار هيدروژني كه مي تواند به داخل فلز نفوذ كند بستگي به خوردگي وpH محيط دارد . آزمايشها نشان مي دهد كه مقدار سولفيد هيدروژن ( H2S ) كمتر از 23 ميليگرم بر متر مكعب و دي اكسيد كربن كمتر از 3%حجمي هيچ مسئله اي را براي فولادهاي سخت كاري شده با سختي برنيل (Brinel hardness ) معادل 33 بوجود نخواهد آورد .
- سولفور
بدليل قابليت حل پايين سولفور در آب ، خوردگي زيادي در اين مورد وجود ندارد .
- مركاپتان
اين ماده بودار به مقدار كم در آب حل مي شود و باعث خوردگي زياد نخواهد شد .
مخازني كه براي CNG طراحي ميشوند، با گازي كار ميكنند كه با استانداردهاي SAE j1616 و CGSB – 3.513 يا ديگر استانداردهاي بين المللي معادل مطابقت داشته باشد. تزريق متانول يا ضديخ به گاز مجاز نيست. بهرحال طراحي مخزن بايد به گونهاي باشد كه مخزن بتواند با دو گاز خشك و تر كار كند.
الف) گاز خشك
ميزان بخار آب در اين گاز حداكثر mg / m3 32 ميباشد ( هنگاميكه گاز در دماي oC 9- و فشار
KPa 20700 قرار گرفته باشد ). در گاز خشك ميزان دو ماده اي که در زير امده است بايستي در حدود مقادير داده شده باشد..
- سولفيد هيدروژن mg / m3 23
- اكسيژن 1% حجمي
ب) گاز مرطوب
در اين گاز ميزان بخار آب ميتواند بيش از mg / m3 32 باشد، اما ميزان موادي كه در زير آمده است بايد در حدود مقادير داده شده بگنجد.
- سولفيد هيدروژن و ديگر سولفيدهاي قابل حل mg / m3 23
- حداكثر گوگرد mg / m3 115
- اكسيژن 1% حجمي
- دي اكسيد كربن 3% حجمي
- هيدروژن 1% حجمي
در شرايطي كه گاز مرطوب است حداقل mg 1 روغن به ازاي هر كيلوگرم گاز لازم است تا لاينرها ، فلنجها و مخازن فلزي را در برابر زنگ زدگي حفظ كند.
در ادامه انواع خوردگي يکنواخت ، خوردگي حفره اي ، خوردگي توام با تنش (SCC ) ، خوردگي شياري ، اثر خوردگي گالوانيکي ، خوردگي سايشي مورد تحليل قرار مي گيرد و راهکارهاي لازم براي جلوگيري و کنترل اين عوامل ارائه شده است.
- خوردگي شياري ( Crevice Corrosion )
اين حالت در شيارها و نواحي روي سطح مخزن که محلولهاي خورنده در اين قسمت ها ساکن شده اند رخ ميدهد.خوردگي شياري در محل تماس لاستيک و فلز شروع شده و پيشروي مي کند . در تسمه هاي نگهدارنده مخزن نبايستي در زير تسمه ها(واشر)مايعات قرار گيرد(به تله نيافتند).
- حفره دار شدن ( Pitting )
در خوردگي حفره اي سطح کوچکي از فلز در اثر عيوب خاصي مانند نقص در پوشش دهي در مجاورت محيط خورنده قرار مي گيرد و با شدت زيادي خورده مي شود . شکل ( 4 ) اين نوع خوردگي شديدا موضعي و متمرکز است که باعث سوراخ شدن فلز مي شود . حفره ها معمولا در جهت نيروي جاذبه رشد مي کنند . حفره دار شدن در اثر يک واکنش آندي اتوکاتاليتيکي مي باشد . مخازن مورد استفاده بايستي از عوامل خورنده محافظت گردند که اين عمل با پوشش مناسب انجام مي گيرد .
شکل4 – خوردگي حفره اي در مخازن نوع اول
- خوردگي بين دانه اي( Intergraular Corrosion )
مرز دانه ها نواحي پرانرژي بوده و از نظر شيميائي فعالتر مي باشند . بدين علت موقعيکه سطح يک فلز در معرض يک ماده خورنده قرار مي گيرد ، مرز دانه ها اندکي سريعتر از سطح دانه ها خورده مي شوند .
همانطور که مي دانيم آلياژها به دو حالت همگن و ناهمگن وجود دارند آلياژهاي همگن در برابر خوردگي مقاومترند زيرا در اين نوع آلياژها حالت گالوانيکي وجود ندارد . بنابراين براي تشکيل يک آلياژ همگن در ساخت مخازن بايستي عناصر تشکيل دهنده اين محلول جامد کنترل گردد. نمونه اي از اين نتايج براي مخازن CNG-2 ساخت شرکت فابردر جدول (4 ) آورده شده است :
جدول – 4 نتايج عناصر تشکيل دهنده در مخازن CNG-2
S+P (%) |
Mo (%) |
Cr (%) |
S (%) |
P (%) |
Mn (%) |
Si (%) |
C (%) |
Cast |
Steelmarker: |
0.012 |
0.18 |
0.96 |
0.004 |
0.008 |
0.74 |
0.29 |
0.36 |
553239 |
AST |
0.01 |
0.18 |
0.99 |
0.003 |
0.007 |
0.73 |
0.27 |
0.35 |
554685 |
AST |
با توجه به ترکيب شيميائي فولادهاي فوق بعنوان مواد مصرفي جهت ساخت مخازن به تشريح مکانيزم مقاومت در برابر خوردگي در اين نوع فولادهاي آلياژي مي پردازيم .
کروم (Cr ) در اين فولادها نقش قرباني را در خوردگي براي محافظت از آهن (Fe ) به عنوان فلز پايه بازي
مي کند . به اين ترتيب که در اثر هجوم اکسيژن به سطح فلز مورد نظر مقدار زيادي اکسيد آهن ( III ) و به ميزان کم اکسيد کروم (III ) ايجاد مي شود اما به علت ميل ترکيبي بيشتر کروم با اکسيژن ، کرم در ترکيب اکسيد آهن ( III ) جايگزين آهن شده و لايه چسبنده و مقاوم به نفوذ اکسيژن را در سطح پديد مي آورد و به اين صورت از فلز محافظت مي کند .
- خوردگي گالوانيکي يا دو فلزي (Galvanic or two metal Corrosion )
اختلاف پتانسيل الکتريکي بين دو فلز غير همجنس که در تماس با يکديگر مي باشند سبب برقراري جريان الکترون بين آنها شده و عامل ايجاد خوردگي گالوانيکي مي گردد. در اين خوردگي اثرات محيطي ( ماننددما ، رطوبت ) و اثر سطح ( نسبت سطح آند و کاتد ) نقش مهمي در سرعت خوردگي دارند .
شکل (5 ) خوردگي گالوانيکي را در مخازن تيپ II که فلز Al با محافظ فولادي در تماس مستقيم بوده است نشان ميدهد. اين نوع خوردگي در مخازن Al مي تواند خرابي ايجاد کند . واشر لاستيکي بايستي حضور داشته باشد و هر محافظي که براي مخزن استفاده مي شود نبايستي در تماس مستقيم با مخزن باشد . بايستي به اين نکته توجه داشت که در هنگام انتخاب قطعات و اتصالات سيستم گاز به نوع جنس مورد استفاده دقت نمود .
شکل -5 خوردگي گالوانيک در مخازن نوع اول و دوم
- خوردگي توام با تنش ( Stress Corrosion )
SCC نتيجه اعمال همزمان تنش هاي کششي و محيط خورنده روي فلز مي باشد. فاکتورهاي مهم در SCC درجه حرارت ، ترکيب شيميائي محلول ، ترکيب شيميائي فلز و کامپوزيت مورد استفاده در مخزن ، تنش و ساختمان فلز مي باشد .
در کامپوزيت الياف شيشه SCC مي تواند رخ دهد. الياف کربن SCC را تحمل نمي کنند . بدترين خورنده ها اسيدها ( مانند اسيدهاي باتري ) مي باشند اما اين اثرمي تواند در اثر بازهاي قوي نيز رخ دهد .يک مثال از SCC در شکل (6 ) نشان داده شده است .
شکل -6 خوردگي توام با تنش در مخازن نوع دوم
اين تنش ها مي توانند باعث ايجاد فشردگي در يک نقطه و عدم فشردگي در نقطه ديگر شوند اين عمل سبب تشکيل يک پيل مي گردد و در آن نقاط داراي فشردگي کم به عنوان آند مساعد جهت خوردگي توسط محيط مي شوند حال آنکه نقاط داراي فشردگي اتمي به عنوان کاتد محافظت مي شوند .
SCC درنتيجه باران هاي اسيدي نمي تواند ايجاد شود چراکه اين اسيدها قدرت کافي ندارند.
راه حل : مخازني که با الياف شيشه پوشانده شده اند نبايستي در تماس با اسيد باشند . باتري ها نبايستي نزديک مخازن قرار داده شوند. اين باتريها براحتي مي توانند کج شده و اسيد سولفوريک ازآنها ريزش کند . در ضمن باتري ها بخار اسيد سولفوريک ساطع مي نمايند که بر روي مخازن مي نشيند . مطمئن شويد که باتري وسيله نقليه در فاصله مطمئن از مخازن کامپوزيت پوشيده شده با الياف شيشه قرار دارند.
بحث و نتيجه گيري
آزمايش هاي مختلفي مانند آزمايش در محيط اسيدي ، آزمايش مخزن تحت شرايط آب شور بر مبناي
استاندارد ISO 11439 تدوين شده اند ولي اکثر آنها توسط استانداردهاي معتبر ديگري نظير NGV2 ، FRP-3 و B51 نيزارائه شده اند . با بررسي آزمايشها ملاحظه مي گردد که مخازن CNG بايستي شرايط ويژه اي را در مقايسه با مخازن تحت فشار معمولي سپري نمايند . سازندگان مخازن CNG و توليد کنندگان وسايل نقليه گازطبيعي سوز بايستي فرآيند کنترل کيفي دقيقي براي بازرسي کليه آزمايشها ي استاندارد را داشته باشند .در صورتيکه مشتريان اينگونه مخازن مواجه با حادثه اي ناشي از ترکيدگي مخازن روبرو شوند اعتماد آنها سلب شده و سياست جايگزيني سوخت CNG با موفقيت مواجه نخواهد شد. لذا سازندگان داخلي و يا تامين کنندگان مخازن بايد تمهيدات لازم براي کنترل فرآيند آزمايشها و يا داشتن تائيديه هاي معتبر سازندگان خارجي را اتخاذ نمايند .